How Does a Robotic Engineering Company Integrate Yaskawa MotoSight Systems?
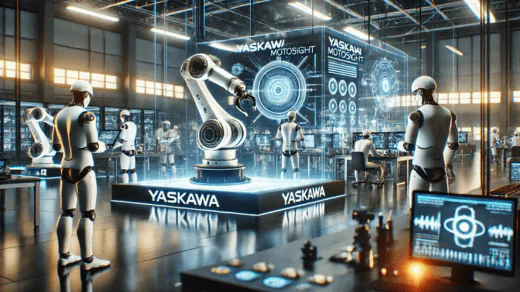
Integrating advanced vision systems like Yaskawa MotoSight into robotics workflows might seem like a complicated endeavor. However, for a robotics engineering company, it’s an exciting opportunity to push the boundaries of automation. These systems enhance precision and adaptability, making robots smarter and more efficient in various industries.
Seamless Communication with Robotic Controllers
Establishing a flawless connection between the Yaskawa MotoSight system and robotic controllers is the backbone of successful integration. For a robotics engineering company in Alabama, this involves configuring the communication protocols to ensure that data flows smoothly between the vision system and the robot. This enables the machine to interpret visual inputs and execute tasks with minimal latency.
The integration process involves programming the MotoSight to align with the robot’s built-in software, ensuring commands are interpreted correctly. By synchronizing these systems, engineers enable robots to respond faster and more accurately to visual cues, which is essential for high-stakes tasks like assembly or inspection. This seamless communication enhances overall efficiency and reduces downtime in automated workflows.
Advanced Vision Calibration for Precision Tasks
Precise calibration of the vision system is a crucial step in integrating Yaskawa MotoSight. A robotics engineering company focuses on adjusting the system’s sensors and cameras to match the specific operational needs of the robot. This calibration ensures the robot can detect objects with high accuracy, even in challenging environments.
Engineers carefully map out the robot’s field of view, accounting for factors like lighting, surface textures, and object positioning. This detailed setup allows the vision system to interpret complex scenes, enabling the robot to perform tasks like picking and placing components or inspecting finished products with pinpoint accuracy. Proper calibration reduces errors and ensures the robot operates efficiently, even in dynamic conditions.
Integration of Real-Time Feedback for Enhanced Accuracy
Incorporating real-time feedback into robotic operations is key to achieving enhanced accuracy. Yaskawa MotoSight systems are equipped to provide instant data on the robot’s performance, allowing continuous adjustments during operations. A robotics engineering company uses this feature to refine tasks and improve precision on the fly.
By processing visual data in real time, MotoSight enables robots to adapt to changing scenarios, such as shifting object positions or unexpected obstacles. This dynamic adjustment minimizes errors and ensures consistent quality in tasks that demand high precision, such as assembling delicate components. Real-time feedback transforms static robotic processes into flexible, intelligent operations.
Custom Software Configurations for Application Versatility
Every industry has unique requirements, and Yaskawa MotoSight’s versatility allows it to be tailored for specific applications. A robotics engineering company in Alabama leverages its expertise to customize the system’s software, enabling it to handle a variety of tasks, from packaging to welding. These configurations ensure that the MotoSight system aligns perfectly with the robot’s intended purpose.
Engineers work closely with clients to understand their workflow needs and design software solutions that enhance productivity. This could include programming the system for specialized tasks or integrating it with existing automation tools. By offering tailored solutions, the robotics engineering company ensures that MotoSight delivers maximum value across diverse use cases.
High-Speed Data Processing for Complex Operations
In environments where speed and accuracy are non-negotiable, high-speed data processing is essential. Yaskawa MotoSight systems excel in this area, enabling robots to analyze visual information and execute commands without delay. Robotics engineering companies rely on this capability to meet the demands of industries like manufacturing and logistics.
The system’s ability to handle large volumes of data in real time allows robots to perform complex tasks seamlessly. For example, in a high-speed production line, MotoSight helps robots identify and sort items quickly, ensuring no slowdown in operations. This level of efficiency boosts productivity and keeps workflows running smoothly, even under tight deadlines.
Alignment with Existing Automation Systems for Workflow Efficiency
Integrating MotoSight systems with pre-existing automation setups is a priority for many organizations. A robotics engineering company ensures compatibility by aligning the vision system with current robotics infrastructure. This integration avoids disruptions and enhances the overall efficiency of automated workflows.
The process includes syncing MotoSight with other tools and platforms, ensuring that all components communicate effectively. By creating a unified system, engineers enable seamless transitions between tasks and minimize the risk of errors. This alignment supports a streamlined approach to automation, helping businesses achieve their operational goals more effectively.
Optimization of Motion Paths Through Vision-Guided Adjustments
One of MotoSight’s standout features is its ability to guide robots in optimizing motion paths. A robotics engineering company uses this capability to improve efficiency and reduce unnecessary movements. By interpreting visual data, the system helps robots calculate the most efficient path to complete tasks.
This optimization not only saves time but also reduces wear and tear on robotic components, extending their lifespan. For tasks that require repetitive actions, such as assembly or inspection, these vision-guided adjustments ensure smoother operations and higher productivity. By incorporating this advanced functionality, robotics engineers create systems that deliver consistent, reliable performance.