Revolutionizing Welding: Collaborative Robots for Arc Welding
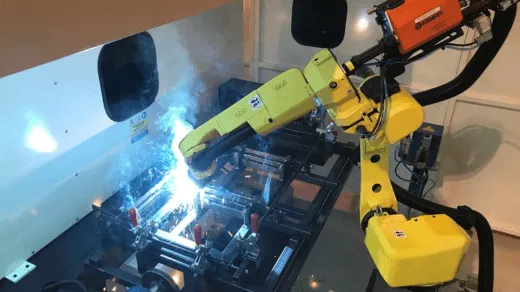
The welding industry has undergone a significant transformation in recent years, thanks to the integration of collaborative robots for arc welding. These advanced robotic systems have revolutionized the way welding tasks are performed, offering increased efficiency, precision, and safety. In this article, we will delve into the world of collaborative robots for arc welding and explore how they are changing the landscape of metal fabrication and manufacturing.
The Rise of Collaborative Robots (Cobots):
Collaborative robots, often referred to as cobots, are designed to work alongside human operators seamlessly. Unlike traditional industrial robots, cobots are engineered to be safe, flexible, and easy to program. This makes them ideal candidates for various applications, including arc welding.
The Advantages of Collaborative Robots for Arc Welding:
- Enhanced Precision: Collaborative robots are incredibly precise in their movements. They can consistently maintain the exact welding parameters, resulting in high-quality welds with minimal defects. This level of precision is especially valuable in industries like aerospace and automotive manufacturing, where weld quality is critical.
- Increased Efficiency: Cobots can work tirelessly without fatigue, significantly increasing welding efficiency and productivity. They can operate 24/7, which is especially advantageous in high-volume production environments.
- Improved Safety: Collaborative robots are equipped with advanced safety features, such as force sensors and collision detection systems. These features allow them to work safely alongside human operators without the risk of accidents.
- Versatility: Cobots are highly versatile and can adapt to various welding tasks and materials. They excel in both simple and complex welding applications, from basic fillet welds to intricate joint configurations.
- Ease of Programming: Programming cobots is user-friendly and does not require extensive technical expertise. This means that even workers without prior robotic programming experience can quickly set up and operate these robots.
Applications of Collaborative Robots in Arc Welding:
- Automotive Manufacturing: Collaborative robots are widely used in the automotive industry for welding tasks. They can efficiently weld components like car frames, exhaust systems, and suspension components.
- Aerospace: In aerospace manufacturing, where precision and quality are paramount, cobots play a crucial role in welding aircraft components, such as engine parts, fuselage sections, and landing gear.
- Heavy Machinery: Cobots are also utilized in the fabrication of heavy machinery, such as construction equipment and agricultural machinery. They excel in welding large and complex components.
- Shipbuilding: Shipbuilding involves the welding of massive structures, and cobots are up to the task. They ensure consistent and high-quality welds on ship hulls and other components.
Selecting the Right Collaborative Robot for Arc Welding:
When choosing a collaborative robot for arc welding, consider the following factors:
- Payload Capacity: Ensure the cobot can handle the weight of your welding equipment and materials.
- Reach and Workspace: Choose a robot with an appropriate reach and workspace to cover the welding area effectively.
- Welding Process: Determine the welding process you need (e.g., MIG, TIG, or stick welding) and ensure the robot is compatible with it.
- Programming Interface: Opt for a cobot with an intuitive and user-friendly programming interface that suits your team’s skill level.
- Safety Features: Verify that the robot has essential safety features, such as collision detection, to ensure safe collaboration with human workers.
In conclusion, collaborative robots for arc welding are ushering in a new era of efficiency, precision, and safety in the welding industry. Their ability to work seamlessly alongside human operators, combined with their exceptional precision and versatility, makes them indispensable in various manufacturing sectors. As technology continues to advance, we can expect to see even greater integration of cobots in welding applications, further enhancing the quality and efficiency of metal fabrication processes.
For more information please visit Cyber-Weld