What Key Performance Indicators Do Control Integrators Typically Focus on During System Optimization?
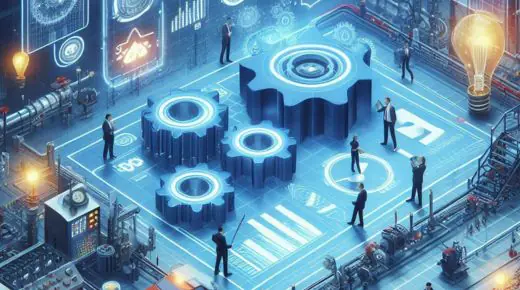
When optimizing complex systems, control integrators rely on a variety of performance indicators to measure success. These KPIs help ensure that systems are running efficiently, accurately, and ready for future demands. Whether it’s improving system uptime or managing energy consumption, these metrics are critical in helping businesses achieve operational goals. Let’s break down some of the key performance indicators that control integrators focus on during system optimization.
System Uptime and Reliability to Ensure Continuous Operations
One of the first things a controls integrator will focus on is system uptime. In many industries, downtime can be incredibly costly, so ensuring that a system runs reliably around the clock is crucial. Uptime is tracked to ensure that the machinery and automated processes are continuously operational, with minimal interruptions. It’s not just about keeping things running—it’s about making sure systems run smoothly and predictably over long periods of time.
Reliability plays hand-in-hand with uptime. By measuring and improving reliability, control integrators can prevent unplanned outages that may stem from system failures or mechanical issues. Predictive maintenance, regular system checks, and optimizing the configuration all contribute to maintaining a high level of uptime. This focus ensures that businesses can trust their systems to perform without hiccups, driving efficiency and output.
Process Efficiency Measured Through Cycle Times and Throughput
Process efficiency is another core KPI that control integrators keep an eye on. The more efficient a process, the faster and smoother it will run, which directly impacts production. Cycle times—how long it takes to complete a specific task—and throughput, the number of items produced within a given time frame, are essential indicators. These metrics reveal how well the system is performing and where there might be bottlenecks slowing things down.
By optimizing cycle times, a control integration specialist can reduce wasted time between tasks, increasing the overall output. Shorter cycle times mean that more products or tasks can be completed in less time, improving both productivity and cost-effectiveness. Meanwhile, throughput analysis helps in pinpointing inefficiencies, allowing for targeted improvements that can enhance overall system performance.
Energy Consumption Metrics for Cost-effective System Performance
Energy consumption is a critical KPI for any company that relies on automated systems. Control integrators look closely at energy usage to ensure that systems are not only efficient but also cost-effective. Monitoring energy metrics can uncover areas where energy is wasted and offer opportunities for optimization that reduce operational costs without sacrificing performance.
Many systems consume energy continuously, and even small inefficiencies can add up over time. By analyzing these metrics, control integration teams can implement strategies such as reducing idle time or optimizing system operations to lower energy consumption. This not only saves money but also contributes to more sustainable practices, which is a growing priority for many companies.
Accuracy and Precision in Automated Tasks to Maintain Quality
When it comes to automation, accuracy and precision are critical for maintaining the quality of the final product. Whether it’s assembling components or executing precise measurements, control integrators focus on ensuring that automated tasks are performed consistently and without error. Any deviation in precision can lead to defects, wasted materials, or rework, all of which hurt efficiency and profitability.
Controls integrators track KPIs related to the accuracy of automated tasks to identify areas where the system may be falling short. With the right adjustments—whether it’s recalibrating equipment or fine-tuning processes—control integration can ensure that tasks are carried out with the highest level of precision. This focus on accuracy ultimately leads to better-quality outcomes, higher customer satisfaction, and fewer operational headaches.
Response Time in Detecting and Addressing System Faults
In automated systems, faults and errors can still occur. How quickly these issues are detected and resolved is another important KPI. Response time is key to minimizing the impact of any disruptions. The faster a system fault is addressed, the less downtime a company will experience, which helps maintain operational flow.
Control integrators optimize systems to have fast detection and response mechanisms in place. This could include automated alerts or built-in redundancies that allow the system to keep running while an issue is being fixed. In some cases, smart technologies such as machine learning can be employed to predict and address faults before they even happen. By reducing the response time, integrators help ensure that a minor issue doesn’t turn into a major problem.
Scalability Potential to Support Future Expansion or Upgrades
Lastly, scalability is an essential KPI that control integrators must consider, especially for businesses expecting growth or system upgrades down the line. A system designed without scalability in mind might struggle to keep up with increasing demand or the need for new functionalities. This is why control integration professionals place a significant focus on ensuring that systems can scale efficiently.
Scalability isn’t just about handling more volume—it’s about doing so without compromising performance. As a system grows, it must continue to perform at the same high level of efficiency, precision, and reliability. By designing systems with future expansion in mind, controls integrators can help businesses stay competitive and adaptable in an ever-changing market.